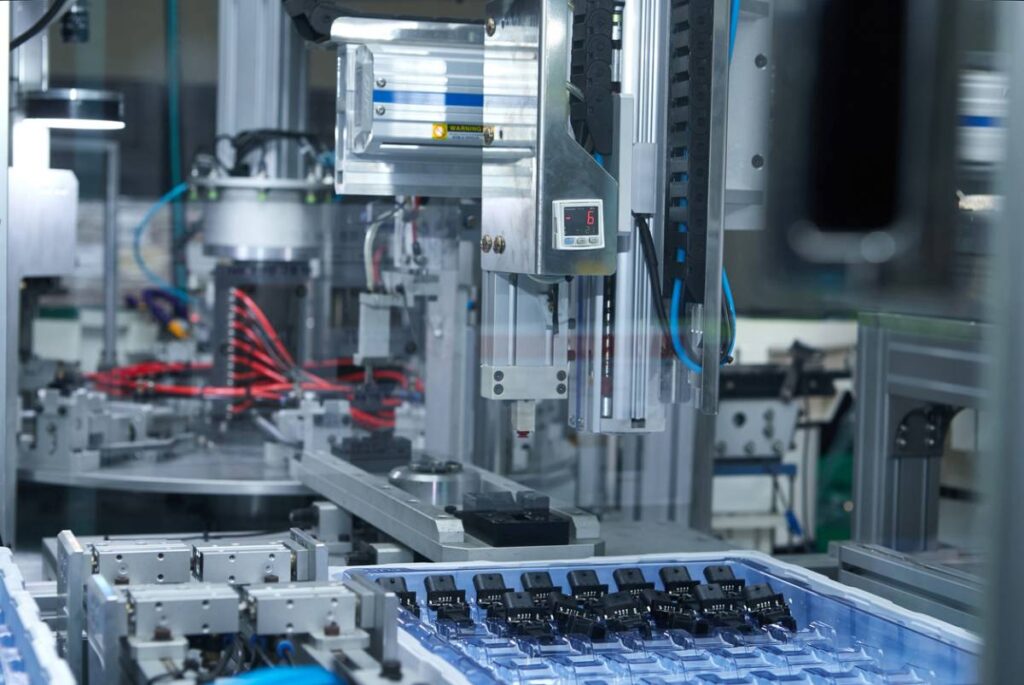
Injection molding is a fascinating procedure that can be useful for a variety of industrial processes. But what is the injection molding process? In short, it is the process of heating a thermoplastic polymer until it becomes liquid and injecting that liquid into a mold so the polymer will take on the mold’s shape. Injection molding is heralded for its versatility and use across many industries. If you would like to learn more about the popular manufacturing method and see how it could be helpful to you, continue reading to uncover more information about the injection molding process.
What Is Injection Molding?
Injection molding is a forming procedure that utilizes molds to create industrial parts. This process is used in a variety of industries. During injection molding, a heated substance is brought to a liquid form, injected into a given mold, and then left to cool. When the substance has cooled in the shape of the mold, it produces a specific industrial part. Injection molding is prized for its ability to produce a variety of different designs and products.
Injection molding machines are generally composed of four different parts, each of which is designed to handle a separate section of the injection molding process. The four sections of an injection molding machine are as follows:
- Cylinder: The cylinder heats the material to be molded
- Nozzle: The material is injected via this device
- Hopper: This feeds the material into the mold
- Mold: The material is poured into this cavity, which produces the final shape
What Is the Injection Molding Process?
The injection molding process follows several steps to its final stage of completion. Generally, the steps for the injection molding process run as follows:
- Resin pellets or granules are poured into the hopper component of the injection mold machine.
- The pellets are then heated and melted inside the cylinder in preparation for the injection molding process.
- The material is then brought through a channel in the machine called the sprue and ultimately into the cavity that creates the mold.
- The material cools and hardens into its final shape.
- Excess material is trimmed from the part.
At this stage, the final product of the injection molding process should be available. This procedure is suitable for creating a number of shapes and devices used in industrial processes.
Advantages of Injection Molding
Several advantages come with using injection molding for industrial design, including:
- Very low amounts of waste material
- Low overhead labor costs
- High color and shape control
- Easy production of complex shapes
- Little post-production finishing required
Many businesses use injection molding as an essential component of their manufacturing processes. You can consult with an expert to see if they believe injection molding is well-suited to your situation.
Disadvantages of Injection Molding
There are some disadvantages that come with the injection molding process, such as:
- Set-up costs are high.
- The process may not be appropriate in situations where only a few pieces of equipment need to be produced.
- There are some restrictions and limitations in terms of what kinds of parts can be produced.
- There can be long set-up times for establishing the molds you are going to use.
Is Injection Molding Right for Me?
It pays to take some time to determine whether using injection molding will be appropriate for your particular situation, as this can help you avoid spending resources on processes that injection molding is ultimately not appropriate for.
Consider the following when trying to determine if injection molding is the appropriate path forward for your project.
- Production quantity: Injection molding is most appropriate in situations where mass production of similar parts is called for.
- Financial: Considering whether the financial cost of setting up injection molding will be offset by the ability to mass-produce parts.
- Design: The overhead cost and overall complexity of the project can be more easily executed if a simple design is used.
Consulting with an expert can help you determine whether or not injection molding is the right tool for your business or project. This can also help you avoid missteps if you are new to this process.
Your Stop for Industrial Advice
Real Seal is a trusted consultant for industries and businesses across the country. If you are interested in utilizing injection molding or learning more about sealing products, contact us today to discuss.